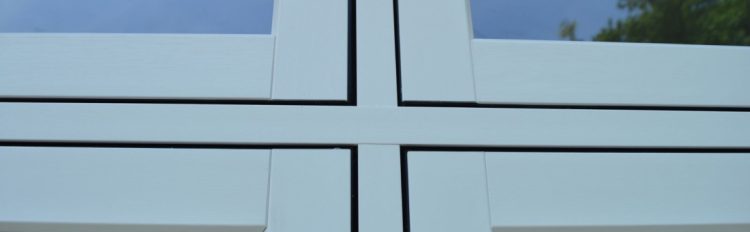
Category: Sash Windows
FLUSH SASHES: WHY COMPROMISE ON PERFORMANCE OR AESTHETICS?
When double glazing first hit the mass market in the 80s, the choice was extremely limited in design and colour. Homeowners with rotting timber windows sacrificed sympathetically designed, coloured frames for white chunky PVC-U, because it offered the durability and energy efficiency they wanted. Flush casements and sliding sashes were swapped for big, bulky, open-out casements. They just don’t look right in period properties (ie, anything before 1914). Inappropriate replacement has been a blight on the look of towns across the UK.
Today the cheapest replacement windows have a limited choice of colours and still don’t look right in period homes. But at the higher end of the market the range is impressive. The demand for colour and appropriate design is chiefly driven by homeowners over the age of 55 – the Haves – who own the majority of the housing wealth in the UK. Largely mortgage-free, if they spend wisely on the right home improvements, the rising value of their property will cover it. But the devil really is in the detail. They care about the appearance of their windows -, but they also want them to be secure, energy efficient and durable. They love the look of timber, but don’t want the maintenance headaches. In this sector, it really is a buyer’s market.
The result is a huge increase in colour, and significant growth in the flush sash market. Having started as a niche style, the timber-look flush sash is set to become mainstream, with a recent study by MRA Research suggesting that nearly 50% of fabricators predict it will become as important as standard casement windows over the next 10 years.
The way flush sashes are jointed is a crucial element of the timber-alternative look. Mechanically jointing the sashes to replicate the traditional look of timber windows achieves that look but at a cost. It needs skilled labour to fabricate and it’s time-consuming, plus impractical and expensive to make at scale. If you plan to grow, welding is the answer.
The standard method for welding PVC-U windows means a 45º corner groove, which spoils the look. It also means that if you choose a coloured, woodgrain foiled window the groove must be ‘coloured in’ with a pen. That’s not the attention to detail homeowners who buy flush sashes require.
System companies have sought to solve this problem using a variety of methods. At the top end of the market, flush sashes are made with mechanical butt-joints and glass-bonded to for strength and integrity. However, this is labour intensive and slow. Other companies use a method of welding that gives a butt-joint look on the outside and a 45º groove on the internal face. Not ideal when homeowners usually see their windows from inside their home! Other options include the Graf Seamless 45º corner weld.
A further option is Timberweld® – a patented method of welding perfect corners, inside and out, to create an authentic timber-look butt-joint effect. Timberweld allows flush sashes to be made with a butt-joint look at scale, cost-effectively. Installation is easier too, as the units aren’t glass-bonded in the factory but installed on site in the usual way.
The Timberweld welding method makes very strong joints. This is particularly relevant at a time when the integrity of mechanical joints is under the spotlight, because rising temperatures and the growing popularity of colour frames could lead to problems with expansion and shrinkage – literally pulling the frame apart in the worst-case scenario. Colour absorbs more heat than white, and dark colours (eg Anthracite Grey) – absorb even more. As flush sashes are invariably foiled – it’s part of the appeal – this is an issue to consider.
Today’s homeowners want it all: stunning looks, and expect the performance to go with it. And fabricators want to supply timber-look windows that last, but in a way that is cost-effective for them in the long term. Neither need to choose or compromise. The technology is here now to give everyone what they want.
For more information on Timberweld® call 01376 534126 or email perfectcorners@timberweld.co.uk.